Breathing Air Tests
Breathing Air - the need for quality testing
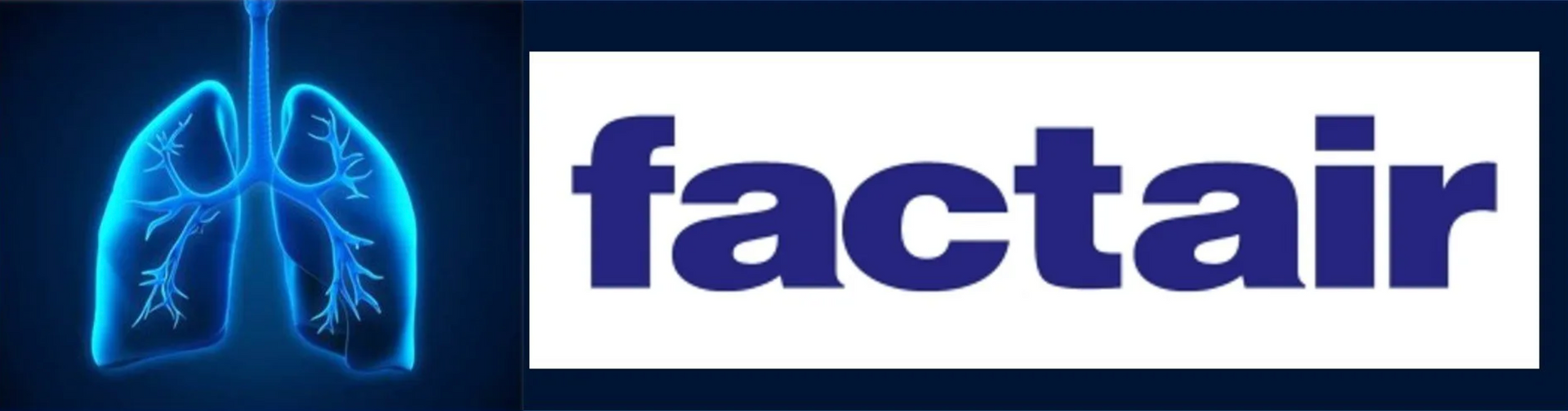
In confined environments where breathing air is provided by a compressor, it is essential to monitor and maintain air supplies regularly. Air supplies from compressors can develop contaminants over time, such as oil, water and dust particles. These are some of the causes and hazards of contaminated breathing air taking from a compressed air system:
- Breathing air filtration has a finite life so after regular use it will fail and cause oil and water to leak into the air supply.
- Airborne pollution including exhaust fumes and dust can be ingested via the air intake to a compressor and not all of this will be removed by standard breathing air filtration.
- High levels of water in breathing air can freeze within the Respiratory Protective Device demand valves causing the air supply to fail.
- It is important to note that when contaminants are breathed in at an elevated pressure, they can have a far greater impact on users than they would at normal pressure.
- The performance of compressor and filtration equipment can change quickly and will affect the quality of breathing air provided. Failure to carry out testing regularly enough can leave users exposed to poor air quality for an extended period.
There is clearly a health risk to the user if they are breathing in contaminated air. Failure to manage this risk can lead to both immediate and long-term health issues such as carbon monoxide poisoning, industrial asthma or chronic obstructive pulmonary disease.
There is clearly a health risk to the user if they are breathing in contaminated air. Failure to manage this risk can lead to both immediate and long-term health issues such as carbon monoxide poisoning, industrial asthma or chronic obstructive pulmonary disease.
Meeting BS EN 12021 regulations
BS EN 12021 is a breathing air quality regulation designed to ensure that breathing air being supplied to an operator is safe and adequate for the respiratory protective equipment they are using.
This regulation requires systems to be regularly monitored, maintained and certified by qualified test professionals.
A comprehensive air quality test will measure levels of:
- Flow
- Oil mist
- Carbon Dioxide
- Carbon Monoxide (CO)
- Water vapour
- Odour and taste
Once the test has been carried out, if the equipment has been shown to adhere to standard BS EN 12021, a Certificate of Testing is produced.
If the air quality fails to meet the current regulations however, the qualified test engineer will recommend appropriate corrective measures. It is advised to test the air again, once these measures have been carried out and before the breathing air point is used again.
Frequency of testing
Low pressure
EN12021 advises that tests should be carried out every three months or more frequently if there have been any changes to the system. HSE guidance states that the frequency of such tests should be based on a risk assessment, but again they should take place at least every three months, and more often when the quality of air cannot be assured to these levels.
High pressure
With high-pressure systems, filter elements have a much shorter life than low-pressure. Therefore, it is recommended that risk assessments for frequency of testing should be based on the expected filter life. Testing should be carried out when new filter elements are fitted and then again when they reach 50% of their life based on the hours run. Subsequent tests would then be dependent on usage with a maximum interval between tests of 3 months.
The final decision on frequency of test is the responsibility of the Employer and needs to not only reflect local legislation but also the task and frequency of use. It should be incorporated into a risk assessment and updated regularly to reflect results from ongoing breathing-air tests to maintain a robust control system.
Record keeping
It is recommended that test certificates and records are kept for 5 years. These can be held in paper or electronic format but should be readily accessible for examination by safety representatives or inspectors.
Protecting employees
All employers have a duty of care to their employees to ensure that the breathing air they are supplied with is adequate for the Respiratory Protection Device they are using and is safe to breathe.
With over 30 years of experience within the compressed air industry and extensive expertise in regulation compliance, BCAS can help employers to meet these responsibilities.
BCAS specialist engineers are Factair certified to test breathable compressed air and ensure it complies with BS EN 12021 standards. We also use high-quality, state-of-the-art testing equipment which is regularly calibrated, to ensure we provide you with the most accurate results.
BCAS can arrange an annual service programme to cover all your Breathing Air Quality Test requirements. Our service plans are cost-effective and convenient and can incorporate the servicing of your compressed air equipment if required.
If you have any questions or would like any further information on BCAS’ breathing air tests, please don’t hesitate to contact us.
A PDF copy of this guide can be downloaded here.