Air leak detection in compressed air
Detect - Repair - Save
All compressed air systems have leaks. The average leakage rate is approximately 25% but some plants lose as much as 80% of their compressed air due to leaks. A single 3mm diameter leak can cost up to £600 a year.
While it may not be practical to eliminate all leaks, it is not difficult to greatly reduce and minimise them. The percentage lost to leakage should be less than 10% of your total compressed air production. A well-maintained system with a proactive leak detection programme in place should allow you to achieve this.
In addition to being a source of wasted energy, leaks can also contribute to other operating losses. By forcing the equipment to cycle more frequently, leaks shorten the life of almost all system equipment (including the compressor package itself). They cause a drop in system pressure, which can make applications run less efficiently, adversely affecting production.
Increased running time due to air leaks can lead to additional maintenance requirements and increased unscheduled downtime. Finally, leaks can lead to increasing compressor capacity unnecessarily.
BCAS specialist engineers have extensive knowledge of compressed air systems and our state-of-the-art ultrasonic testing equipment provides accurate results to allow us to identify and quantify all air leaks – many of which are not audible. Our comprehensive leak assessment and repair programme can vastly improve the operation and efficiency of your facility and generate significant financial savings.
The benefits of an air leak detection audit:
- Reduced energy consumption
- Cost savings
- Short payback period
- Less environmental impact
- Improved reliability
- Prolonged equipment life
- Production lines operate more efficiently and to their optimum capacity
- A pro-active process that can be planned and timed
- Equipment runs more quietly leading to more comfortable working conditions
Common causes of leaks in a compressed air system:
While leakage can come from any part of the system, the most common problem areas are:
- Couplings, hoses, tubes, and fittings (tubes and push-to-lock fittings in particular)
- Disconnects: O-rings required to complete the seal may be missing.
- Filters, regulators and lubricators (FRLs): Low first-cost, improperly installed FRLs often leak.
- Open condensate traps: Improperly operating solenoids and dirty seals are often problem areas.
- Pipe joints: Missed welds are a common problem.
- Control and shut-off valves: Worn packing through the stem can cause leaks.
- Point of use devices: Old or poorly maintained tools can have internal leaks.
- Flanges: Missed welds are a common problem.
- Cylinder rod packing: Worn packing materials can cause leaks.
- Thread sealants: Incorrect and/or improperly applied thread sealants cause leaks.
- Bag houses
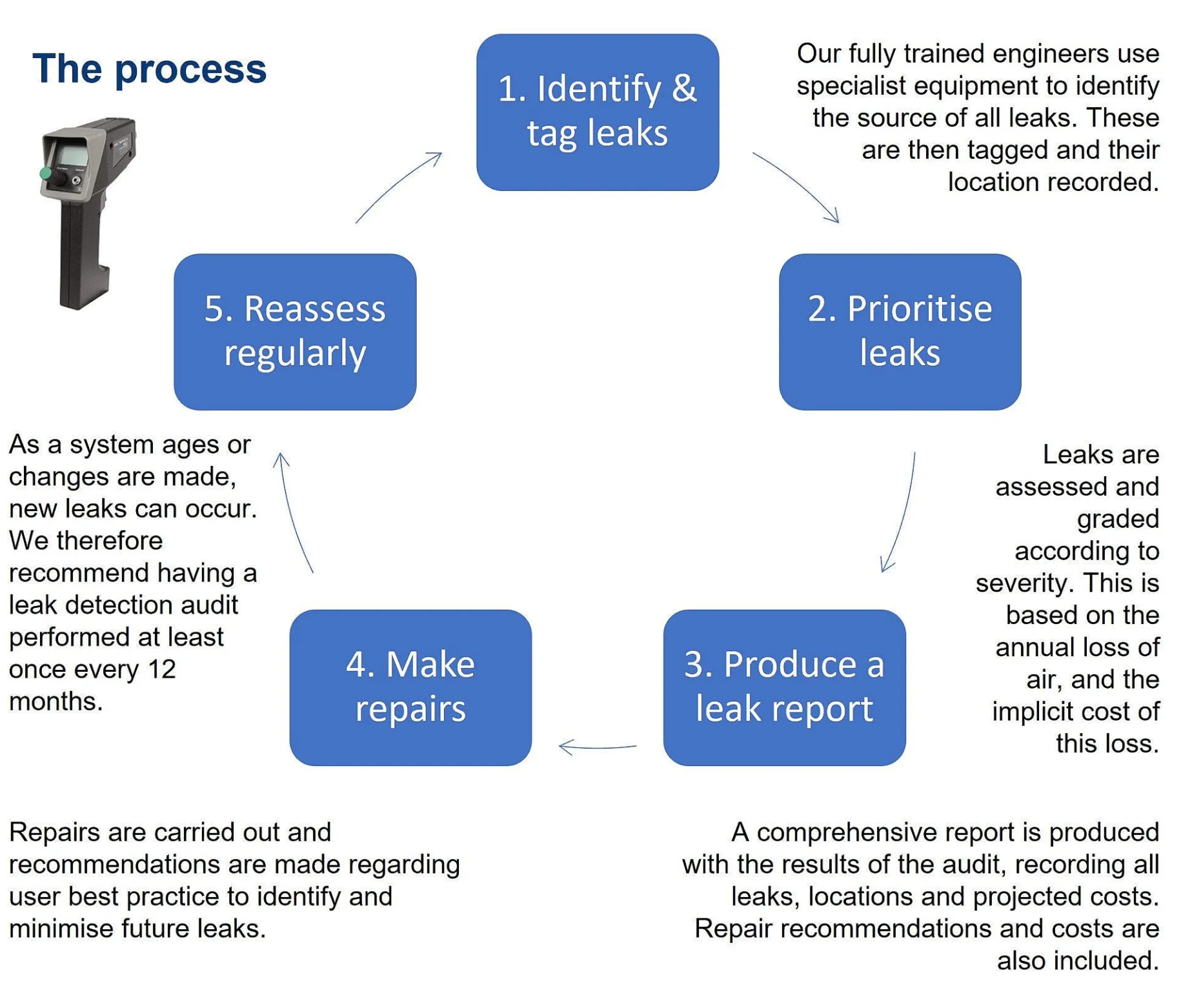
BCAS specialist engineers use the latest ultrasonic testing equipment to identify and quantify all air leaks, many of which cannot be easily detected by the human ear.
Once a system has been logged and leaks have been identified and tagged, a detailed report is produced, outlining the extent of the losses and the recommended works.
And if you wish, BCAS can then carry out the necessary leak repairs. In fact, BCAS can manage the entire process for you and can even incorporate it into an overall energy efficiency programme for your compressed air system.
To find out more about how we can help you to maximise the efficiency of your compressed air equipment and reduce your energy costs,
contact the BCAS team today.